Die Casting Parts in Aluminium and Magnesium
For over 35 years, we have been manufacturing advanced die casting parts in aluminum and magnesium.
We specialize in prototypes and small batches for new development projects, standing out from the competition with our high-quality parts and fast, reliable delivery schedules.
What we offer
- Open communication and reliable delivery schedules
- Price-competitive solutions
- Die Casting up to 3000 Ton Clamping Force
- Combined manufacturing in Ningbo and Denmark
- High-Tech CNC Machining facilities
In addition to the casting process, we also offer the following services:
- Design support (For high pressure die casting).
- Flow Simulations
- CNC Machining (20 high-tech machining centers)
- Laser engraving
- Leak testing
- Friction stir welding
- Impregnation
- Measurement reports
- Technical cleaning
- Small assembly tasks
Would you like to discuss a new project or learn more about what we can offer ? Then please don’t hesitate to contact Stig. He is a nice guy and would be happy to help !
Stig Dahl
Key Account Manager, Die Casting
Phone: (+45) 40 50 55 24
Mail: sd@formkon.dk
Die Casting - Technical Specifications
MACHINE SIZES – MAXIMUM CLAMPING FORCE
Aluminium: 3,000 ton
Magnesium: 2,500 ton
Zinc: 500 ton
STANDARD ALLOYS
• Aluminium AlSi9Cu3(Fe) – EN AB-46000
• Aluminium AlSi12(Fe) – EN AB-44300
• Aluminium AlSi12Cu1(Fe) – EN AB-47100
• Aluminium AlSi10Mg(Fe) – EN AB-43400
• Aluminium AlSi10MnMg – EN AB-43500
• Magnesium AZ91
• Magnesium AM50
• Magnesium AM60
• Zinc Zamak 5 (ZnAl4Cu1)
Other alloys on request.
STANDARD CASTING TOLERANCES
DIN EN ISO 8062-3
SUITABLE NUMBERS
50-5.000 pcs.
FINISH
Finish as a die cast item.
Die casting of prototypes - the process in brief
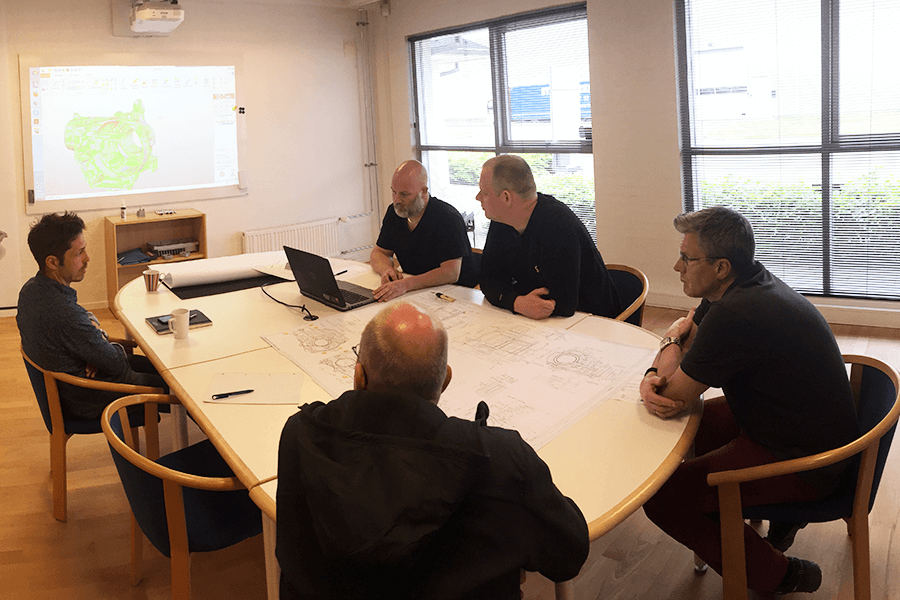
Professional partners
Formkon has more than 35 years of experience in the design and engineering of die-cast parts. That’s why we can advise our clients effectively, saving everyone time and money.
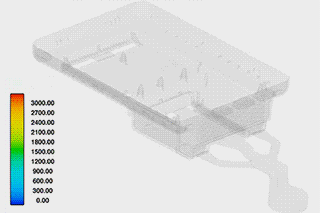
Casting simulations
For complex parts we use advanced flow simulations. These simulations enable an optimal start – with minimized error risk and optimized lead time.
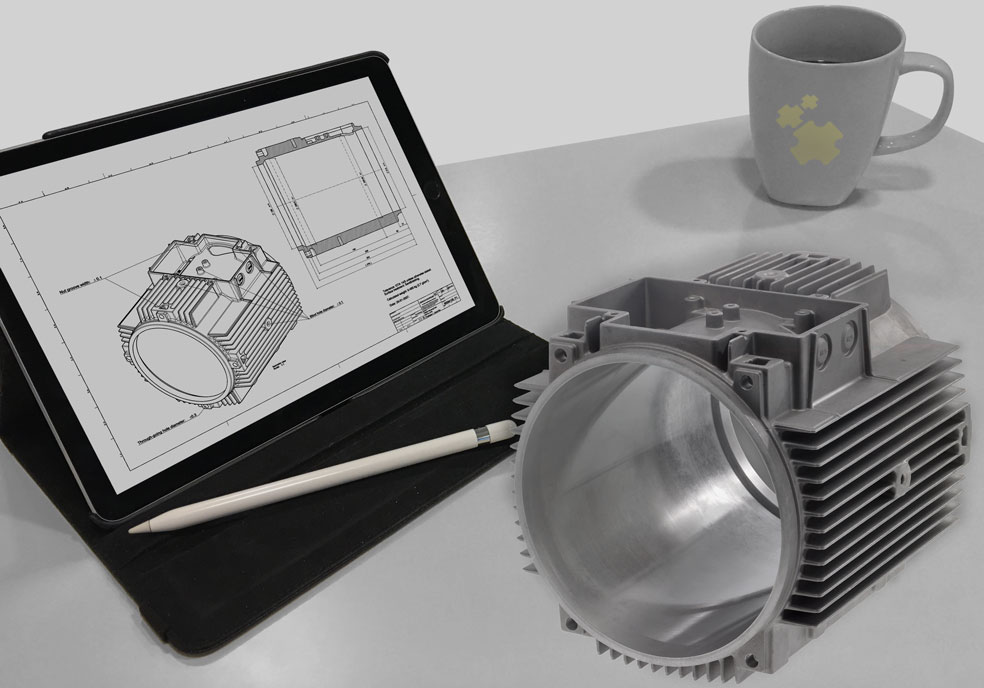
Prototype tools
In order to save time, we work exclusively with prototype tools in soft steel grades. The die cast parts are then produced on die casting machines up to 3000 tons clamping force.
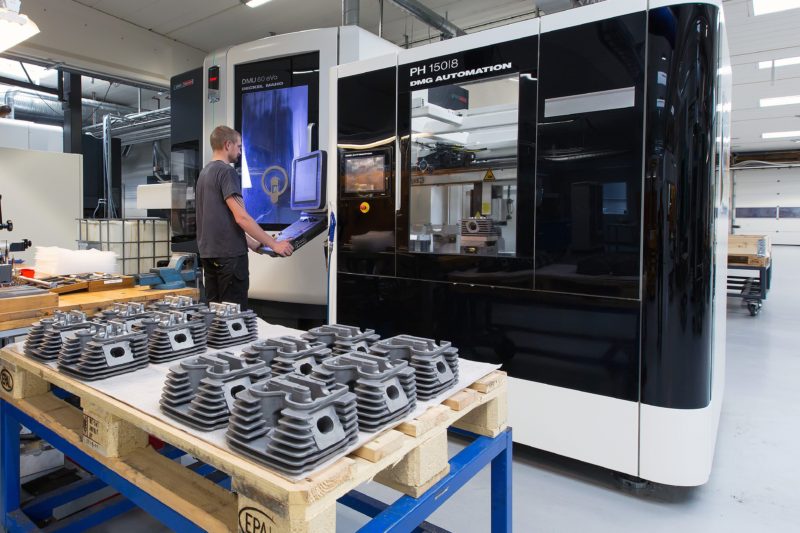
CNC machining
After casting, CNC machining can take place. Thanks to state-of-the-art technology and machinery, we can process very complex and demanding components.
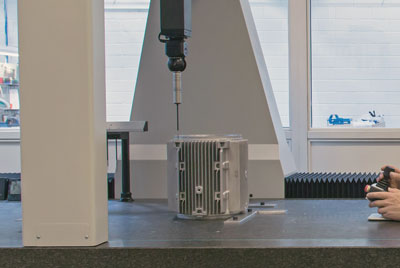
Quality control
Before shipping the items, we can measure and check them to ensure that they fully meet the customer’s requirements.
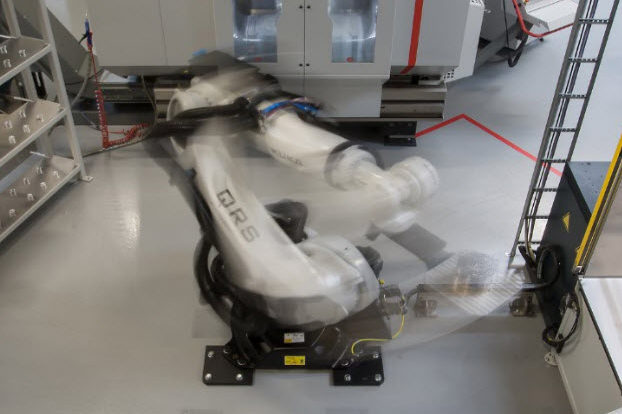
Lightning fast delivery times
The complete concept is optimized to quickly deliver the right quality. This concerns the complete procedure from offer to delivery. For us, quick reactions and close dialogue are important, so that together we optimize the lead time.